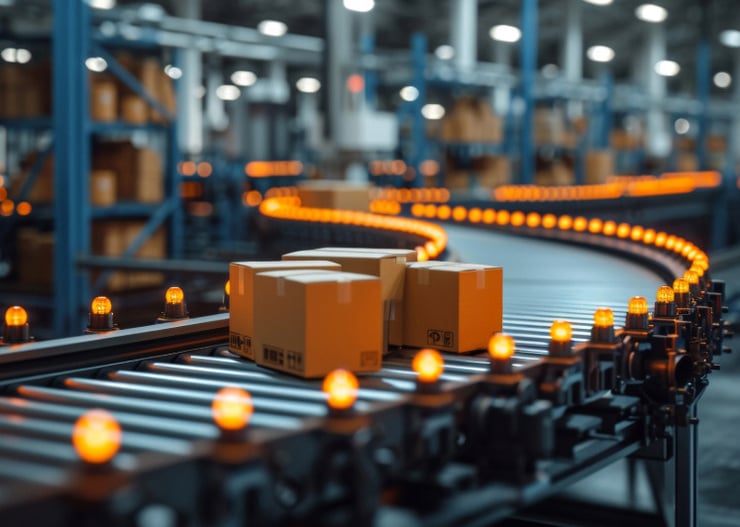
What is a factory production order and what is it used for?
A manufacturing order is an essential part of a plant's production process. This order contains detailed information on the steps required to produce a product, the resources required, the raw materials, the expected lead times or the necessary work instructions. The production order contributes to efficient production management and the achievement of objectives.
In a production order, you'll find all the information and instructions needed to produce a product:
- Order number and creation date
- Product information (name, code, quantity to be produced, production dates, etc.)
- Raw materials required
- Manufacturing instructions: how to prepare raw materials, assemble components, check packaging, etc.
- Quality control instructions
- Equipment required
- Human resources (workshop manager, production operators, quality controller, etc.)
A production order is usually written by a planning or production manager, who ensures that all the right information is included in the order.
The production order, crucial to your production management
A production order is an essential part of a plant's output, as it enables :
- Production planning: the order specifies when, where and how each product will be manufactured.
- Allocate resources: orders specify the resources required for manufacturing operations (human, material, raw materials, etc.).
- Track costs: orders collect production-related costs, enabling you to track, control and avoid cost overruns.
- Control quality: production orders document product specifications and standards.
- Manage deadlines: the order includes production schedules for each stage of the process. This helps to meet delivery deadlines, minimize delays, etc.
- Reduce errors: the order contains all the instructions on how to manufacture a product.
- Analyze performance: data collected from orders can be used to analyze production performance and identify areas for improvement.
- Inventory management: the order groups together the quantities of raw materials required to manufacture the product. This makes it easier to manage stocks and avoid excesses and shortages.
- Respect regulatory compliance: a production order can be used as a compliance document, attesting that the product has been manufactured in compliance with current standards and regulations.
What are the key functions of MES software for managing your production orders?
By combining certain functions, MES software optimizes the management of manufacturing orders, providing real-time visibility, improving production efficiency, guaranteeing product quality and contributing to more effective overall plant management. Plant managers stay informed at all times about what's going on in the factory.
With an MES solution on the factory floor, you benefit from essential functions for organizing production orders. Planning, management and monitoring functions.
MES software enables you to plan production according to demand, priorities and available resources. It manages the creation, modification and deletion of production orders. Details of each order, such as product, quantity, resource requirements and specifications, are recorded.
The software automatically allocates the necessary resources to each order, and defines order sequencing, i.e. the order in which production orders are to be carried out, according to priorities, production constraints and deadlines.
Every day, operators receive their production orders from MES software. Although the process may vary according to the way the system is configured in the plant and the IT tools available, MES software manages :
- Order creation and allocation
- Operator notification via dashboard, e-mail or SMS alert, or printed work order
- Access to instructions with production steps, procedures, safety instructions, etc.
- Work execution, with relevant data recorded (cycle times, production quantities, problems encountered, etc.) and archived (traceability, production times, production quantities, reports, etc.).
- Real-time monitoring, enabling managers to assess the progress of the production order.
How do you manage your production orders with MES AVEVA software?
Factory Software offers a range of software solutions designed to optimize the management of your production orders:
AVEVA PlanetTogether (Advanced Planning and Scheduling): AVEVA APS is dedicated to advanced production planning and scheduling. Start by planning manually, or enter your production constraints and rules into the system to automate the scheduling process.Once you have the data you need, you can create schedules in seconds.
AVEVA MES Operations : Bring order to all your production operations - from a single production workshop to an organization with many production sites. Replace disparate applications or manual methods with a single, easy-to-implement system for managing your operations. Your teams can access job planning, material BOMs, product specifications, production order instructions, inventory levels, product genealogy, traceability and all this according to the key elements of your production - all in a contextualized way. Managing the execution of production orders guarantees that products are manufactured to specifications, and enables you to collect detailed information on execution and associated material flows in real time.
AVEVA Batch Management : The AVEVA Batch Management solution provides extremely flexible management of all batch operations. It is essential for managing production orders in the factory, as it optimizes and rationalizes the production process. AVEVA Batch Management software helps to plan production orders according to available resources, priorities, deadlines and production capacities. It enables production orders to be grouped into batches, optimizing resource utilization while minimizing the risk of downtime between product changeovers. With AVEVA Batch Management, you can optimize and control production by grouping production orders into batches.