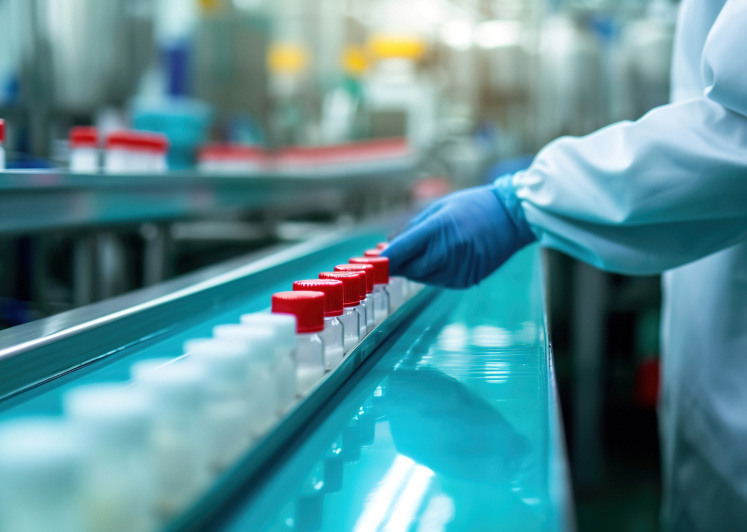
What is factory traceability and product genealogy?
In-plant product traceability is the ability to follow the evolution of a product from the receipt of raw materials to its delivery as a finished product. You know the origin, history and destination of each manufactured product, and you guarantee product quality, safety and conformity.
Product traceability is essential to meet regulatory requirements and industry standards, to guarantee product quality and safety, to facilitate product recalls in the event of quality problems, to improve inventory management and to ensure customer satisfaction.
For its part, product genealogy is the ability to track the history of a product throughout its life cycle, from conception to end-of-life. It is indispensable for knowing the different stages of production and transformation of a product, as well as the raw materials, components, machines and operators involved in its manufacture. Product genealogy is often associated with product traceability, however, it goes further by making it possible to track the complete history of a product, including its design, specifications, drawings, modifications and updates.
Traceability, like product genealogy, can be achieved using a variety of tools and technologies, including MES software.
How does MES software help manufacturers control product traceability and genealogy on a daily basis?
1/ Real-time data collection
MES software collects data in real time from a variety of equipment and sensors installed at different production points. This equipment is connected to the plant's internal network, enabling data transfer.
Data collected includes information on production processes, production rates, cycle times, downtime, quality problems, maintenance operations, and raw material and finished product inventories. This data is then processed and analyzed by the MES software to provide production managers with real-time indicators of production performance, and to feed into production monitoring dashboards.
2/ Track batches and serial numbers
MES software must be able to track product batches and serial numbers throughout the production process, recording each step and associating the data with a unique identifier. This enables rapid identification of products in the event of a recall or quality problem.
3/ Recipe and production formula management
The software must be capable of managing recipes and production formulas, ensuring traceability of ingredients, production parameters and test results.
It must also enable the management of product variants, recording differences in recipes and production formulas for each variant.
4/ Inventory management
The software must be able to manage raw material and finished product inventories in real time, allowing traceability of stock movements and available quantities.
5/ Regulatory compliance
The software must be able to adapt to current regulations and standards, such as FDA regulations, ISO standards or industrial quality standards.
6/ Product recall management
The software must be able to manage product recalls in the event of quality or safety problems, enabling rapid traceability of the products concerned.
Since MES software enables products to be tracked throughout the production process, from receipt of raw materials to delivery of the finished product, if a problem is detected on a batch of products, the information gathered by MES software can be used to quickly identify the batches concerned, know the location of the products, and determine the cause of the problem.
7/ Tracking defective products
By recording production data in real time, MES software can help to quickly identify faulty products and track their progress through the production process. This enables immediate corrective action to be taken to avoid product returns and recalls.
MES software analyzes the data collected and identifies deviations from quality standards, technical specifications or production targets. Once a deviation or problem has been identified, MES software is used to trace the history of products associated with the problem. Affected products can be identified using batch numbers, barcodes or other unique identifiers associated with the products, then production managers take appropriate action such as stopping production, quarantining defective products or removing defective products from the production line.
How can you ensure product traceability and genealogy with an AVEVA MES solution?
Factory Software offers several AVEVA software packages to ensure traceability and product genealogy in the factory:
AVEVA MES: This software enables you to monitor and control every stage of the production process, from receipt of raw materials to delivery of finished products. It enables you to collect real-time data on production operations, track product batches and serial numbers, ensure regulatory compliance, and facilitate product recalls in the event of quality problems. More about AVEVA MES >
AVEVA Recipe Management: This solution enables you to manage and control recipes and production formulas, ensuring traceability of ingredients, production parameters and test results. The software also enables you to manage product variants, control the quality of raw materials and minimize production costs. More about AVEVA Recipe Management > AVEVA Work Tasks
AVEVA Work Tasks: This software acts as a workflow management platform for AVEVA MES solutions. AVEVA Work Tasks provides the ability to manage, execute and document all processes. It thus replaces all manual processes and paper documents by automatically managing routine operations as well as conditional and critical operations. More about AVEVAWork Tasks >
AVEVA APS - Planet Together: This software will help you plan and optimize your production processes. From tracking your raw material stocks to final delivery, you can plan and monitor the entire production chain. From your equipment to your operators and even your tools, everything can be planned and optimized according to the optimization rules you define. The software also enables you to plan simulation scenarios, or to see in advance whether you can meet an order by simulating its planning.