Operational Excellence… mit vielen Kollegen habe ich darüber gesprochen und gerne definiert das jeder auf seine Weise. Ich verstehe darunter, ein hohes Maß an Zuverlässigkeit der Anlagen zu erreichen und Anwender in die Lage zu versetzen, die Effizienz in der gesamten Produktions- und Unternehmensorganisation, einschließlich der Lieferkette, zu maximieren. Das ist eine große Aufgabe! Und am besten fängt man klein an. Und digitale Systeme helfen Anwendern beim Aufbau einer soliden Anlagenstrategie als Grundlage für das Erreichen von Operational Excellence.
Ein erfolgreicher Plan muss Menschen, Prozesse und Anlagen berücksichtigen. Ich arbeite dazu gerne mit einem 5-Schritte-Plan:
1. Stellen Sie ein funktionsübergreifendes Team zusammen, um einen mehrdimensionalen Plan zu erstellen
Echte Operational Excellence wird nicht von einer einzelnen Person oder einem Team erreicht. Sie erfordert das Fachwissen und die Erkenntnisse aller, die Einfluss auf die zu verbessernden Aktivitäten haben. Zu den Stakeholdern können Mitarbeiter aus den Bereichen Betrieb, Wartung, Technik, Compliance, Geschäftsstellen und anderen Bereichen gehören. In dem Bewusstsein, dass die Entwicklung von Operational Excellence einige Zeit in Anspruch nehmen wird, müssen Unternehmen die aktuellen Abläufe auf Lücken und Verbesserungsmöglichkeiten analysieren und dabei in einigen wenigen Schlüsselbereichen beginnen.
Dazu können Produktionsprozesse, Betriebs- und Wartungsverfahren, Teamfähigkeiten, Anlagenzustand und Lebenszyklus, unterstützende Systeme und Daten oder andere Bereiche gehören. Zu den allgemeinen Überlegungen für einen mehrdimensionalen Plan gehören:
- Produktionsprozesse: Verwenden Sie Metriken, die definieren, ob die Produktionsraten und -qualitäten den Erwartungen entsprechen und ob die Anlagen die Spezifikationen erfüllen.
- Menschen: Untersuchen Sie, ob die richtigen Informationen, Verfahren und Schulungen vorhanden sind, damit das Personal erfolgreich eingeführt werden kann und zu effektiven Teammitgliedern wird und auch im Laufe der Zeit effektiv arbeitet.
- Anlagen: Ermitteln Sie die Kosten für die Instandhaltung sowie unerwartete Steigerungen oder kritische Ausfälle mit dem Ziel, die betrieblichen Anforderungen mit den Instandhaltungsanforderungen in Einklang zu bringen.
- Systeme und Daten: Sind die richtigen Systeme vorhanden, um zuverlässige und zeitnahe Daten an das Personal zu liefern, unabhängig davon, ob es sich vor Ort in der Fabrik befindet oder aus der Ferne arbeitet?
- Geografie & Kultur: Gibt es bei Unternehmen mit mehr als einem Standort Unterschiede in den Praktiken und beim Personal, die berücksichtigt werden müssen, und können Best Practices zwischen den Standorten übertragen werden?
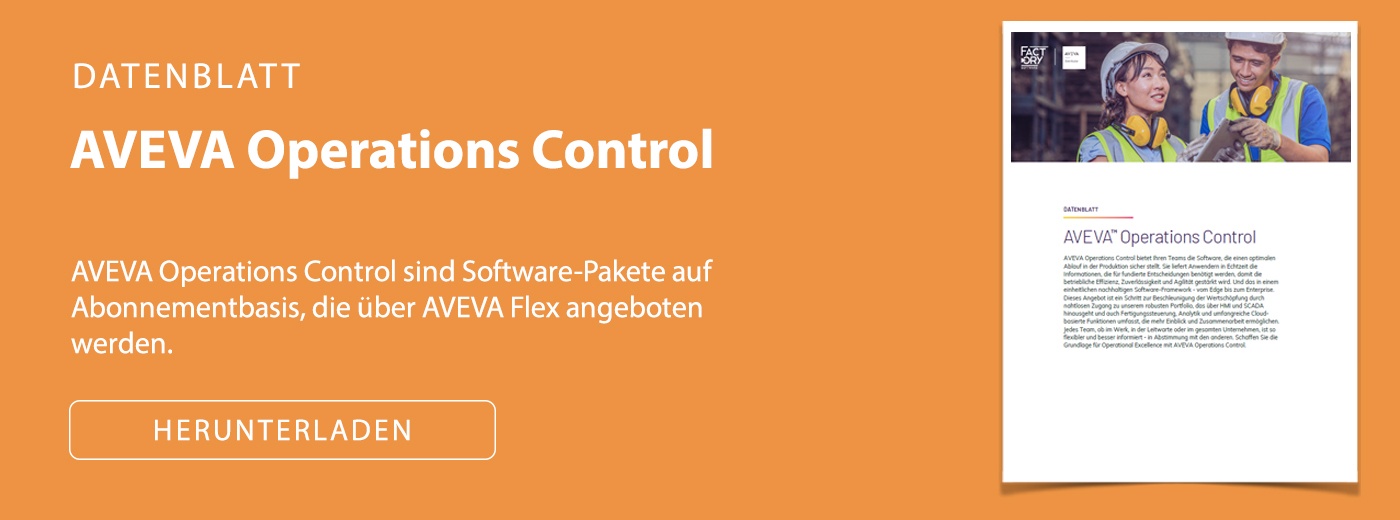
2. Definieren Sie die Benchmarks, Strategie und Ziele
Verwandeln Sie den Plan in eine Strategie zum Erreichen der Betriebs- und Leistungsziele. Nutzen Sie Vergleiche mit Branchenkollegen und Benchmarks, um sicherzustellen, dass die Ziele in Einklang mit der Branche stehen und angemessen sind. Richten Sie die Strategie an den Risikobereichen des Unternehmens aus, wie z. B. Verfügbarkeit von Anlagen, Einhaltung der HSE-Richtlinien, Produktivität und Rentabilität. Identifizieren Sie dann spezifische Schulungen und Technologien, die zur Verfolgung der Strategie implementiert werden müssen. Vielleicht benötigen die Betriebsteams zum Beispiel ein Kollaborationstool, um die Kommunikation bei sozialer Distanz zu erleichtern.
3. Ausrichten der Strategie auf eine digitale Transformation
Während fast jede Branche die Notwendigkeit hat, digital zu werden, befindet sich jede Organisation in einem anderen Stadium der Einführung digitaler Technologien zur Bewältigung betrieblicher Aufgaben. Einige Aktivitäten werden vollständig digital sein, und die meisten werden zumindest durch digitale Technologien unterstützt. Mit dem Plan und der Strategie in der Hand sollten Sie überlegen, welche digitalen Technologien bereits vorhanden sind oder aufgerüstet oder hinzugefügt werden sollten, um den Erfolg zu ermöglichen.
Darüber hinaus beginnt dieser Schritt auch mit der Bewertung der Kosten, die mit der Ausführung jeder Aktivität verbunden sind. Legen Sie die Prioritäten für die Implementierung neuer Prozesse und Technologien auf der Grundlage der erwarteten Kapitalrendite (ROI) fest und wägen Sie die Risiken ab, die mit dem Zeitplan, den Produktionsanforderungen, der Beschaffung von Ausrüstung, der Verfügbarkeit von Personal und anderen Faktoren verbunden sind, um die am unmittelbarsten umsetzbaren Punkte zu bestimmen.
4. Priorisierung von Risiko, Kosten und Leistung
Erstellen Sie eine Aktionsliste und einen Zeitplan und delegieren Sie bei Bedarf Verantwortlichkeiten an Stakeholder und Sourcing-Partner. Definieren Sie klare Key Performance Indicators (KPIs) und andere Metriken, um die Ausführung der Aufgaben zu messen und zu verfolgen.
5. Was haben Sie gelernt und was wollen Sie besser machen
Bei der Ausführung einer Strategie ist es immer wichtig, Abweichungen zu bewerten und die gewonnenen Erkenntnisse zu prüfen, um den Plan zu iterieren und zu verfeinern und so eine kontinuierliche Verbesserung auf dem Weg nach vorne zu ermöglichen.
Wie sieht Ihre Strategie aus?